Chemical treatment
COOLING WATER TREATMENT
Cooling water treatment chemicals play a key role in maintaining the optimal performance and durability of cooling systems.
Cooling water is used in a variety of industrial plants, including energy, manufacturing, chemical industry and other areas where it is necessary to control the temperature of equipment and processes.
Cooling water treatment chemicals are used to prevent the formation of deposits, corrosion and biological growth in cooling water systems.
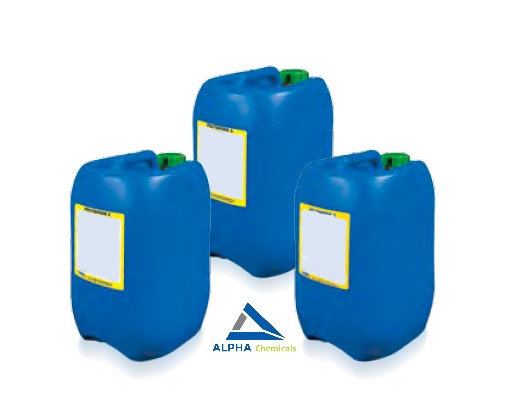
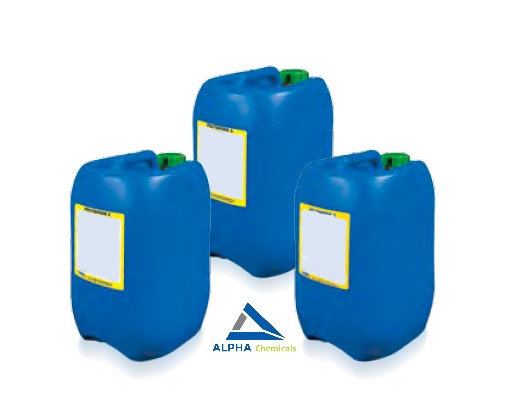
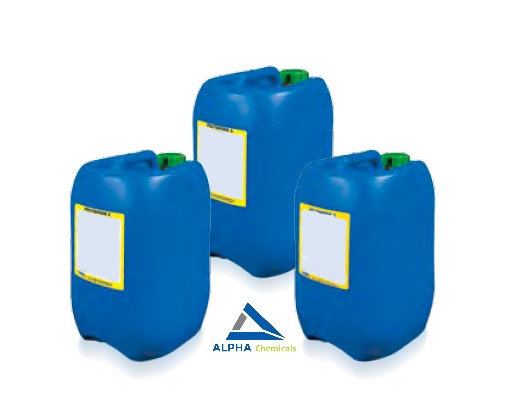
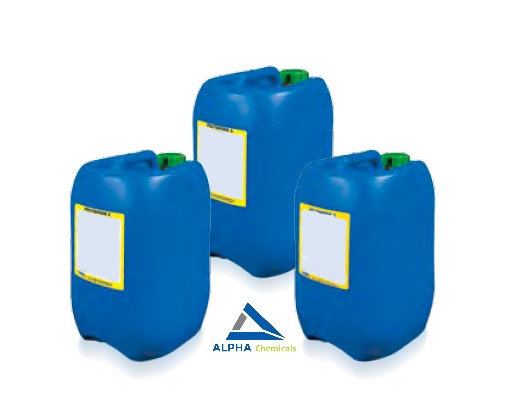
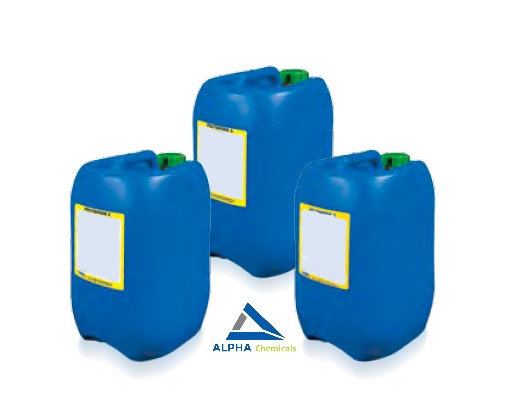
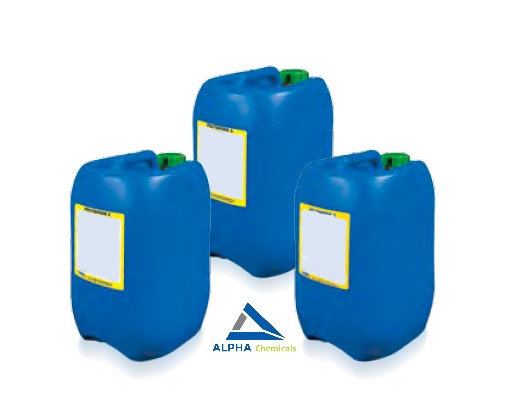
BOILER WATER AND STEAM TURBINE TREATMENT
Boiler water and water for steam turbines play a key role in power plants by ensuring reliable and efficient steam generation to generate electricity.
However, the presence of corrosive salts, deposits, oxidations and microbiological organisms can lead to damage to the equipment and a decrease in efficiency.
Chemicals for the treatment of these waters play a vital role in preventing problems and maintaining optimal system performance.
Problems
Boiler water and water for steam turbines are exposed to high temperatures, pressures and chemical reactions, which can lead to serious problems such as corrosion, deposits, reduction of efficiency and microbiological contamination.
These problems can cause damage to equipment, decreased efficiency and increased maintenance costs.
Decision
Boiler water and steam turbine water treatment chemicals provide preventive and protective measures to prevent the above problems.
These chemicals are carefully dosed into the water system to create protective layers on surfaces, stabilize pH, prevent deposits and corrosion, and control the growth of microorganisms.
Corrosion inhibitors
Corrosion is a serious problem in boilers and steam turbines because high temperatures and pressures can cause rapid degradation of metals.
Corrosion inhibitors are substances that are added to water to form a protective layer on metal surfaces. This layer prevents direct contact of metals with water and reduces the risk of corrosion. Corrosion inhibitors often contain inorganic salts that react with metals and create a passive layer.
Dispersants and deposit inhibitors
Mineral deposits and salt deposition can reduce water flow, increase energy consumption and reduce efficiency. Dispersants keep particles suspended in water, preventing their deposition and stacking. Deposit inhibitors prevent the formation of salt deposits on the inner surfaces of pipes and equipment.
pH stabilizers
A properly balanced pH ensures that the water is neither too acidic nor too alkaline, which can reduce the risk of corrosion and deposits.
Balanced water pH is crucial for corrosion prevention. PH stabilizing chemicals help maintain water in the optimal pH range, preventing corrosion and damage to equipment.
Oxidizers
Oxidants are used to control the presence of oxygen in water, which reduces the risk of corrosion. Removing oxygen helps to keep metal surfaces in good condition.
Biocidal treatments
Microbiological organisms such as bacteria and algae can cause biofilm formation and corrosion. Biocidal treatments are used to suppress the growth of microorganisms and maintain clean water.
Redox regulators
Redox water potential plays an important role in maintaining water stability and preventing corrosion. Redox regulators help maintain balanced redox potential.
Water treatment chemicals are dosed strictly according to prescribed guidelines and maintained continuously to ensure optimal system performance. Water monitoring and regular testing allow timely dosing adjustment and maintain the safety, reliability and efficiency of power plants.
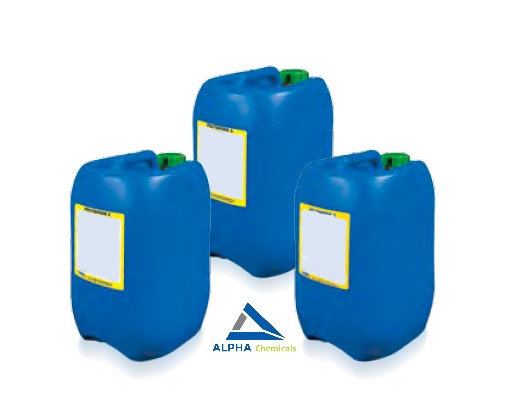
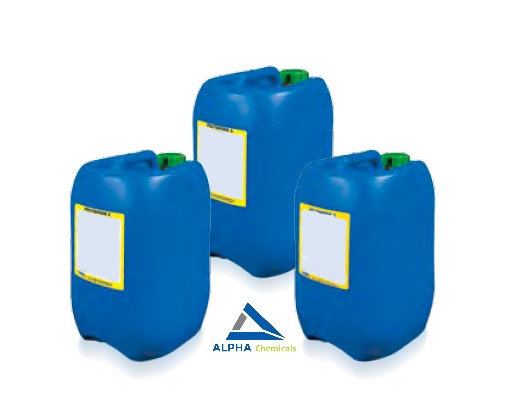
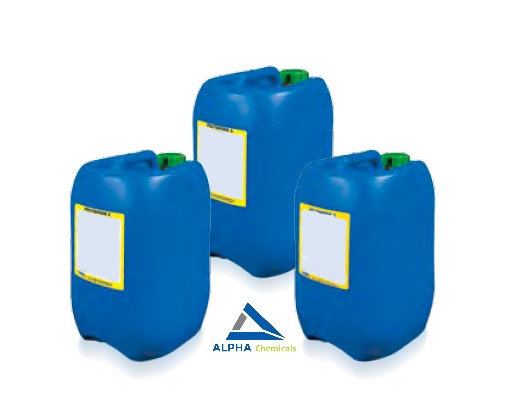
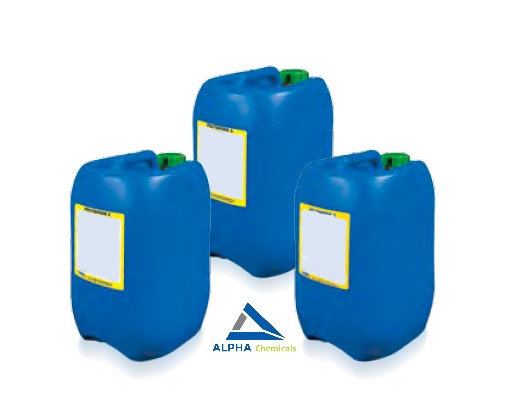
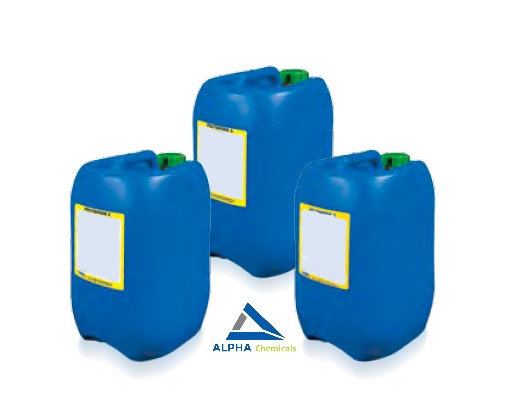
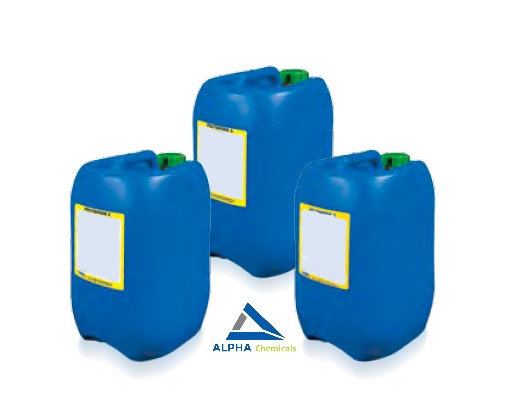
TREATMENT OF MEMBRANE SYSTEMS (Reverse Osmosis / Desalination)
High-quality and efficient operation of membrane systems such as reverse osmosis, Ultrafiltration, Nanofiltration, seawater desalination or MBR- membrane bioreactors need effective chemical treatment.
Problems during work that are more common are clogging of membranes, formation of deposits on modules (algae, mucus, biology..), cracking or degradation of membrane fibers due to the input quality of water. With the application and the correct dosage, you ensure the quality of equipment operation, durability, eliminate repairs and downtime.
ANTISCALANTS
A necessary group of products to prevent the formation of deposits and deposits on membranes. To prevent the deposition of mineral salts, the most common of which are calcium carbonate (CaCO3) and calcium sulfate (CaSO4).
The inlet water to membrane filtration systems, if not treated with appropriate means to prevent the formation of deposits, will quickly clog and block the flow of permeate and thus reduce the efficiency and quality of operation of the system.
DECOLANTS
Group of chemical products for removal i.e. the decomposition of chlorine from the incoming water coming to membrane systems. The process of membrane systems when taking water with chlorine create damage to membranes and their gradual degradation of materials. Depending on the system, there are options to eliminate chlorine through an activated carbon filter or by dosing dechlorant into the feed water system.
BIOCIDES AND CLEANERS
Chemical products for preventing or cleaning membrane modules from microorganisms and bacteria. Due to the very process where chlorine is eliminated from the water before contact with membranes , there is a probability of the appearance of bio deposits on the modules when standing the system. The use of funds successfully eliminates the occurrence or created deposit of microbiological deposits on the system.
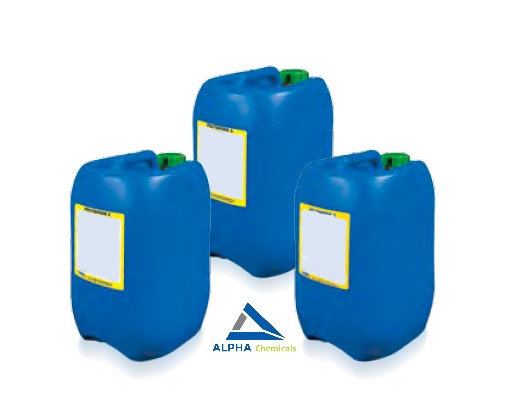
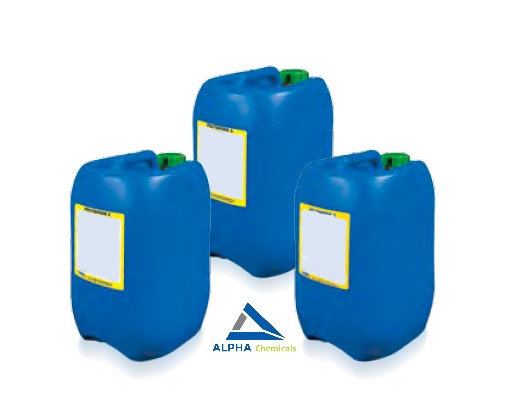
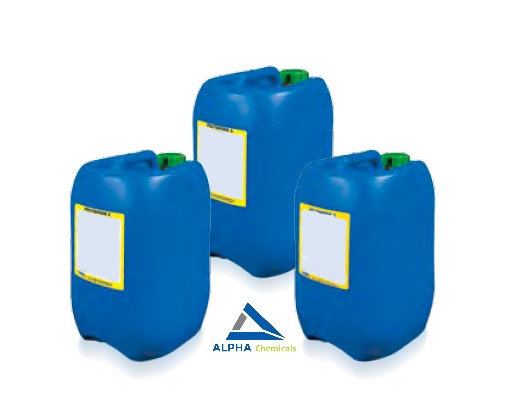
The main objectives of cooling water treatment chemicals include:
CORROSION PREVENTION
Problem:
Corrosion is a serious problem in cooling systems because water can react with metals, causing damage and shortening the life of the equipment.
Decision:
The addition of corrosion inhibitors, chemicals that create a protective layer on metal surfaces, prevents direct contact of water with metals.
Corrosion inhibitors provide passive protection and reduce corrosion rate, thereby extending the life of equipment and reducing maintenance costs.
PREVENTION OF SEDIMENTS AND DEPOSITS
Problem:
Mineral deposits can form due to the precipitation of mineral salts from the cooling water, which reduces water flow and system efficiency.
Decision:
Adding dispersants and scale inhibitors helps prevent salt build-up and keep pipe and equipment surfaces clean.
Dispersants help disperse salt particles, and deposit inhibitors reduce salt adhesion on surfaces, thereby maintaining water flow and reducing cleaning needs.
BIOCIDAL ACTION
Problem:
Microorganisms such as bacteria, algae and fungi can grow in cooling systems, creating a biofilm and reducing water flow.
Decision:
The use of biocidal chemicals suppresses the growth of microorganisms and prevents the formation of biofilms.
Biocidal chemicals suppress the development of microorganisms and keep the surfaces of the system clean, thereby reducing the risk of clogging and corrosion.
WATER STABILIZATION
Problem:
Fluctuations in pH and mineral concentrations can cause deposits and corrosion in cooling systems.
Decision:
The addition of stabilizing chemicals maintains the pH value and mineral concentration of the water within optimal limits.
PH stabilizers and deposition inhibitors help keep water in a stable and balanced state, reducing the risk of damage.
WATER DISPERSION
Problem:
Concentrated particles and deposits can collect in cooling water systems, reducing flow and efficiency.
Decision:
Dispersing chemicals help keep particles in suspension and prevent them from settling.
Dispersants keep particles dispersed in water, thereby reducing the risk of plaque and clogging of the system.
Properly selected chemicals for cooling water treatment should be compatible with system materials, effective in low concentrations and safe for the environment and humans.
Regular monitoring and analysis of the quality of cooling water ensures that chemicals are dosed according to the needs of the system, ensuring optimal performance, durability and safety.