…water and just water…
CWG - CLEAN WATER GROUP
O nama
Naš široki spektar rješenja bazirana na stručnosti i iskustvu omogućuju realizaciju svake vrste tretmana vode, ali i daje mogućnost našim korisnicima da modificiraju, promijene ili poboljšaju postojeću opremu. Specijalizirani isključivo na „vodu“, sa tradicijom preko 40 godina CWG je posvećen pružanju rješenja, tehnologije i proizvoda za tretman, pročišćavanje i filtriranje voda.
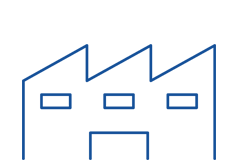
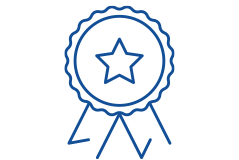
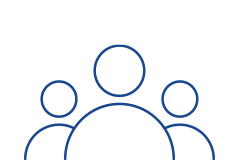
NAŠA RJEŠENJA
NAŠI PROIZVODI
Sve informacije su vam dostupne sada na jednom mjestu ...water and just water...